Vacuum Leak Testing
- Home
- On-site Services
- Leak testing
- Vacuum Leak Testing
Leak Testing
Other on-site services
Contact
Would you like us to send you a quote? Or do you have a question about this test? Let us know and we will contact you as soon as possible!
Vacuüm test voor lekdetectie
Industrial leak testing and leak detection are not simple matters. Even the choice of the appropriate testing method and associated measuring equipment needs to be carefully considered. The ideal method for a specific application depends on many factors.
Both the sensitivity of the applied testing method and the size of the leaks to be detected are important when testing an object or a vacuum system.
Leaks in vacuum systems and components are often specific defects that can have a significant impact on the safety and performance of systems and installations. Many systems and products will be less reliable if they contain leaks. Normen zoals API 607 worden toegepast om de betrouwbaarheid en veiligheid van systemen in uitdagende sectoren, zoals de petrochemische industrie, te waarborgen.
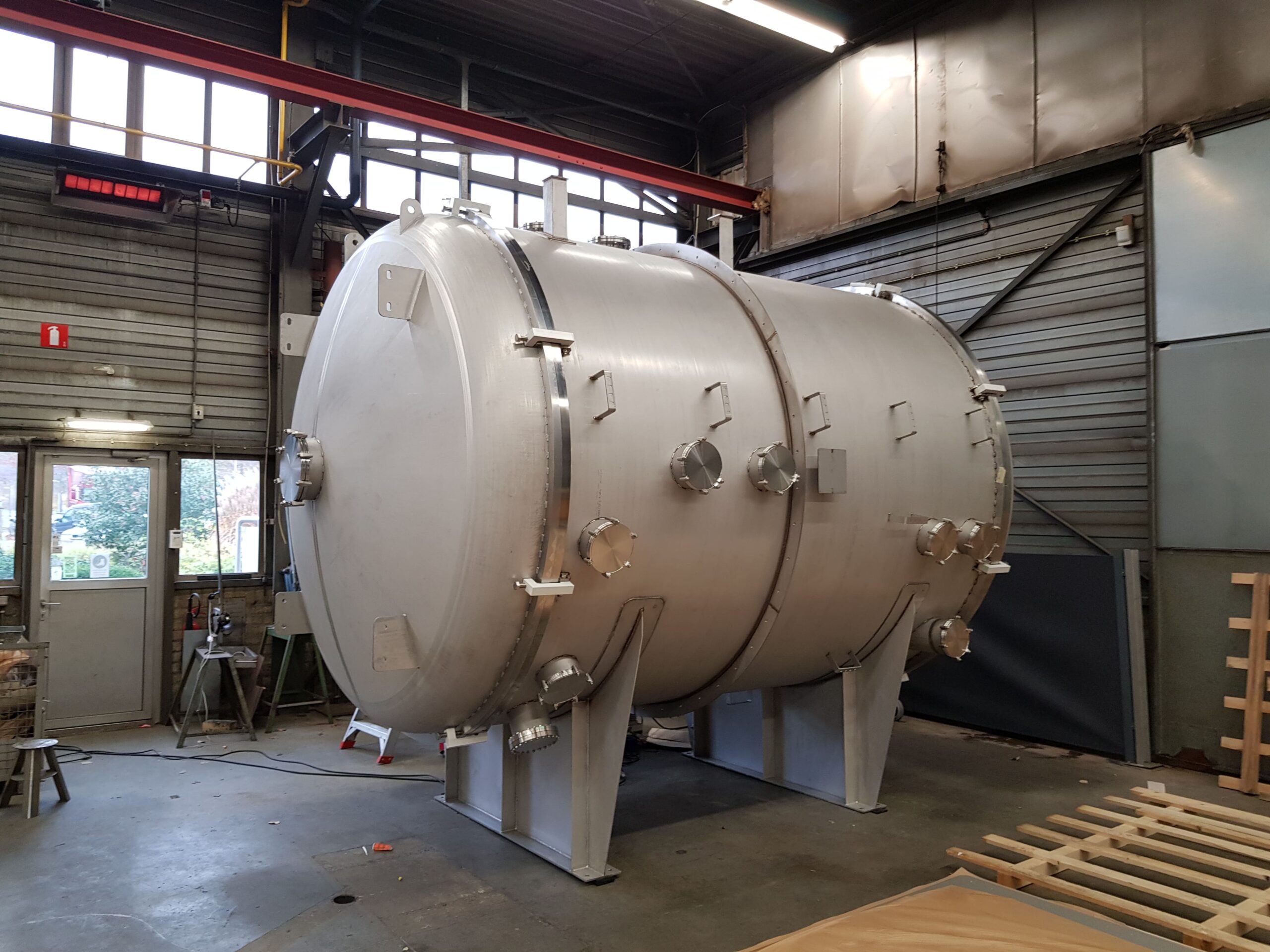
ITIS can apply the following techniques for its customers, among others:
Helium vacuüm testen van objecten
Met de helium snuffelsonde techniek wordt het te testen object inwendig geëvacueerd waarna het uitwendig ‘besproeid’ wordt met een tracer gas. Het meest gebruikte test gas voor deze methode is helium. Het tracer gas dringt het object binnen door de aanwezige defecten en wordt gedetecteerd m.b.v. meetapparatuur, soms in combinatie met een afzonderlijke vacuüm pomp. Een kritiek punt van de vacuüm methode is niet alleen het bepalen óf een object lekt, maar ook de exacte locatie van het lek.
Luchtinbreuk testen van vacuümsystemen
Air ingress testing identificeert luchtinfiltratie in vacuümsystemen, die de prestaties en kwaliteit van productieprocessen negatief kunnen beïnvloeden. ITIS past deze methode toe om lekken effectief op te sporen en systemen optimaal te laten functioneren.
Air ingress (vrij vertaald: binnen dringen van lucht) in een vacuüm systeem kan lijden tot een verminderde product kwaliteit, productie verlies, schade aan de omgeving of gevaarlijke situaties. Het helium lektesten van uw vacuüm systeem kan uw productie snelheid aanzienlijk verhogen, zal de integriteit van componenten verifiëren en uw vacuüm systeem effectiever laten functioneren.
Our measuring equipment allows technicians to perform leak tests while the installation is in operation, without the need to isolate sections for testing.
Helium is "sprayed" around parts of the vacuum system, while a mass spectrometer continuously measures the vacuum system and detects (low) concentrations of test gas in case of a leak.
In some cases, an extractor with a permeable membrane is used to connect the test equipment to the vacuum system. This membrane ensures that no water vapor or liquids come into contact with the measuring equipment.
Although finding leaks in vacuum systems presents a series of challenging problems, our technicians have developed a test solution specifically designed for the demanding conditions encountered in vacuum systems.
Vacuümbox testen
Het doel van vacuüm box testen is het lokaliseren van lekken in druk afscheidingen welke niet direct op druk gezet kunnen worden. Dit wordt gerealiseerd door het aanbrengen van een zepige oplossing op een lokaal deel van het afscheidingsoppervlakte en het creëren van een drukverschil over dit oppervlak. Wanneer er een defect aanwezig is in het test oppervlak, zal het ontstaan van belletjes (als gevolg van doorstroming van gas door de oplossing) de plaats van eventuele lekkage aanduiden. Deze methode is een van de meest toegepaste test methodes om lekkage en defecten op te sporen en wordt doorgaans gebruikt voor het testen van de wanden, bodems en daken (laswerk) van tanks.
Contact
Do you have a question?
Would you like us to send you a quote? Or maybe you have a question about one of our services. Fill in the form below and we will contact you as soon as possible.
ITIS Goes
-
Columbusweg 64
4462 HB Goes - +31-113 568515
- info@itis-nl.com