Overpressure Leak Testing
- Home
- On-site Services
- Leak testing
- Overpressure Leak Testing
Leak Testing
Other on-site services
Contact
Would you like us to send you a quote? Or do you have a question about this test? Let us know and we will contact you as soon as possible!
Overpressure Leak Testing
Overpressure Leak Testing
During a pressure leak test, a higher pressure is created inside the object being tested compared to the surrounding environment. In the case of a leakage, the medium (tracer gas) inside the object will escape into the surrounding environment, and the leaks can be detected using the appropriate techniques.
Direct Sniffing with Tracer Gas
In most cases of pressure leak testing, helium gas is used as the tracer gas to detect leaks. The principle is based on creating an overpressure inside the object being tested by filling it with helium gas. A sniffing probe is then used to scan the surface of the object for the presence of helium. If there is a leak, the helium gas will escape and can be detected by the sniffing probe. This allows for the identification of the leak location. This principle enables quick and direct detection of leaks using helium or other tracer gases, such as hydrogen.
Accumulation Method with Tracer Gas
In helium leak testing using the accumulation method and a sealed or fixed volume, helium gas is used as the tracer gas to detect leaks. The principle involves filling the sealed or fixed volume with helium gas and then waiting and accumulating. If there is a leak, the helium gas will slowly escape and accumulate in the sealed or fixed volume. Over time, the concentration of helium can be measured using a helium detection system, such as a mass spectrometer. A higher concentration of helium indicates a leak in the object. This method allows for the detection of the presence and size of leaks through the accumulation of helium gas.
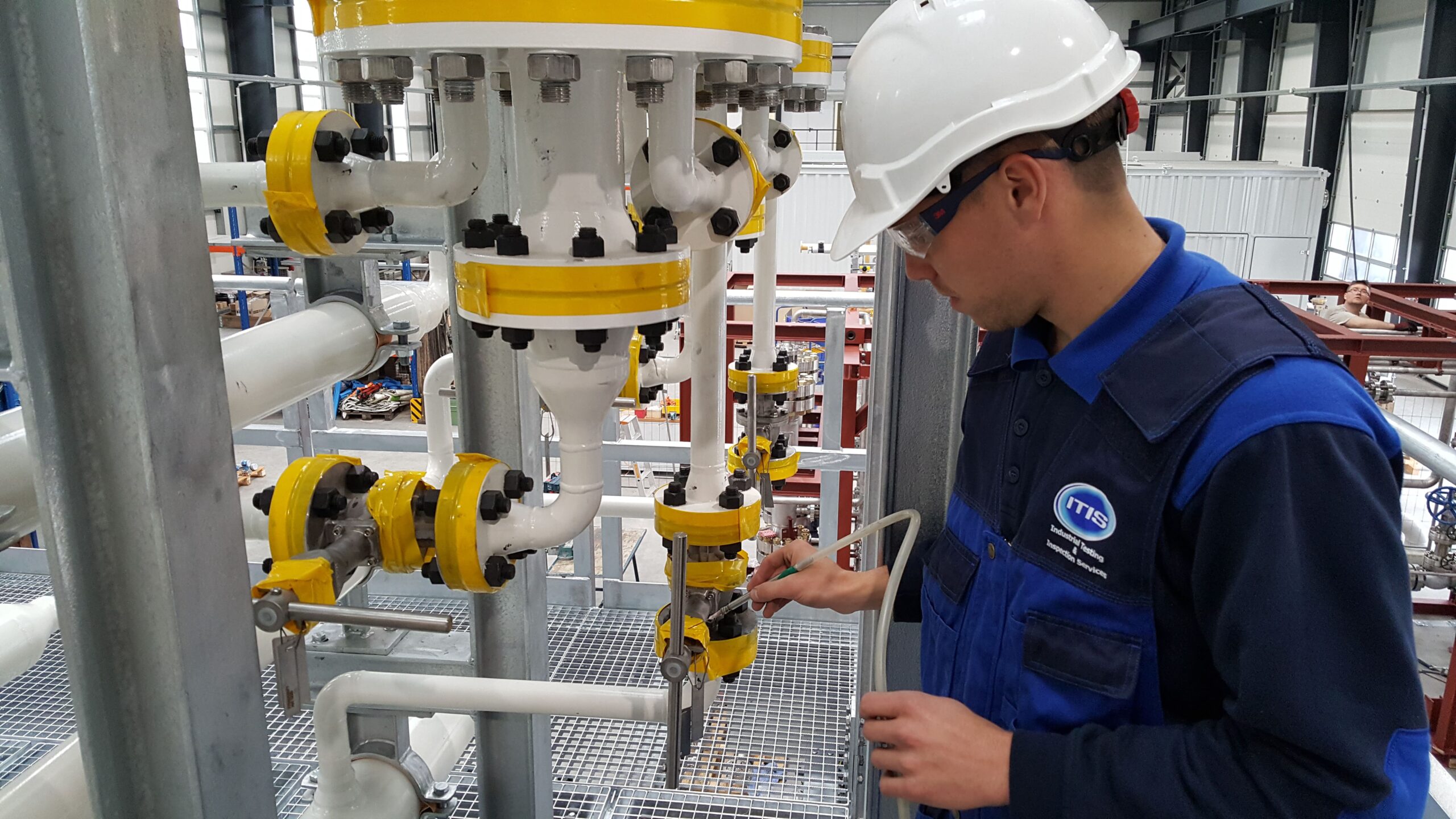
Ultrasonic Leak Testing Ultrasonic leak testing in pressure systems utilizes ultrasonic sound to detect leaks. The principle is based on the fact that when there is a leak, turbulence and eddies occur in the medium flowing through the leak. This turbulence generates ultrasonic sound that is beyond the audible range of humans. Using an ultrasonic detection device, this sound can be captured and analyzed to determine the location and size of the leak. In this way, leaks in pressure systems can be discovered by detecting the ultrasonic sound generated by the leak.
Foam/Soap Bubble Testing Foam/soap bubble testing, also known as the soapy test, is a simple method for detecting leaks in various applications, such as gas pipelines, compressed air systems, water pipes, and seals.
In this test, a soap mixture is typically applied to the surface or weld joint being tested using a spray bottle. If there is a leak, gas will escape, resulting in the formation of bubbles at the leak location. By visually inspecting where the bubbles form, the location of the leak can be identified.
It is important to note that this testing method is typically used for relatively larger leaks, as small leaks may not be visible to the naked eye. For detecting very small leaks, more advanced testing methods such as helium leak testing are often employed.
Contact
Do you have a question?
Would you like us to send you a quote? Or maybe you have a question about one of our services. Fill in the form below and we will contact you as soon as possible.
ITIS Goes
-
Columbusweg 64
4462 HB Goes - +31-113 568515
- info@itis-nl.com